Scaling sustainable carbon fibre production: A breakthrough in lignin-based innovation
Lignin, a waste product from cellulose production, can be used to improve the sustainability credentials of carbon fibre. Professor Jonny Blaker has demonstrated production at pilot-scale, paving the way for industrial application.
Carbon fibre is a critical material for industries such as aerospace and automotive, prized for its strength and lightweight properties. However, traditional carbon fibre production relies on costly, petroleum-based materials, driving up costs and environmental impact.
Lignin – a widely available by-product of cellulose production, with around 70 million tonnes generated annually – offers a promising, sustainable alternative. Typically treated as waste or burned for energy, lignin has untapped potential for high-value applications, including next-generation carbon fibre manufacturing.
From lab to pilot scale
Industry partner Lixea has been collaborating with Imperial College London, where Dr Agi Brandt-Talbot and Professor Milo Shaffer developed a patented technology to convert lignin into carbon fibre at a small lab scale (1ml production). The process leveraged two key innovations:
- Ionic liquid technology – dissolving various lignins while allowing the liquid to be recycled after fibre formation.
- Polyvinyl alcohol (PVA) – a non-toxic, biodegradable polymer used as a spinning aid.
This approach not only enables the production of high-lignin-content fibres (75-90%) with excellent structure and yield but also significantly reduces costs. By replacing petroleum-based precursors with lignin and ionic liquids – both renewable, lower-cost, and less toxic materials – production costs could be reduced.
51¸£ÀûÉç’s ability to scale up
To validate this technology at scale, Dr Joanne Ng from Imperial College joined forces with Drs Dominic Wales and Umar Muhammad, researchers at 51¸£ÀûÉç and Royce Application Scientists, led by . Together the team created a pilot-scale demonstration at the Fibre Technology Platform, at the Henry Royce Institute, using its wet spinning line. Lignin was sourced from Lixea’s pilot plant, which uses the same ionic liquid to extract lignin from wood waste, ensuring process alignment with the company’s existing technologies.
The team tested three different lignins – two from spruce sawdust, and one from bagasse, a by-product of sugar production – with the bagasse-derived lignin proving most effective, enabling continuous fibre spinning at pilot scale for the first time.
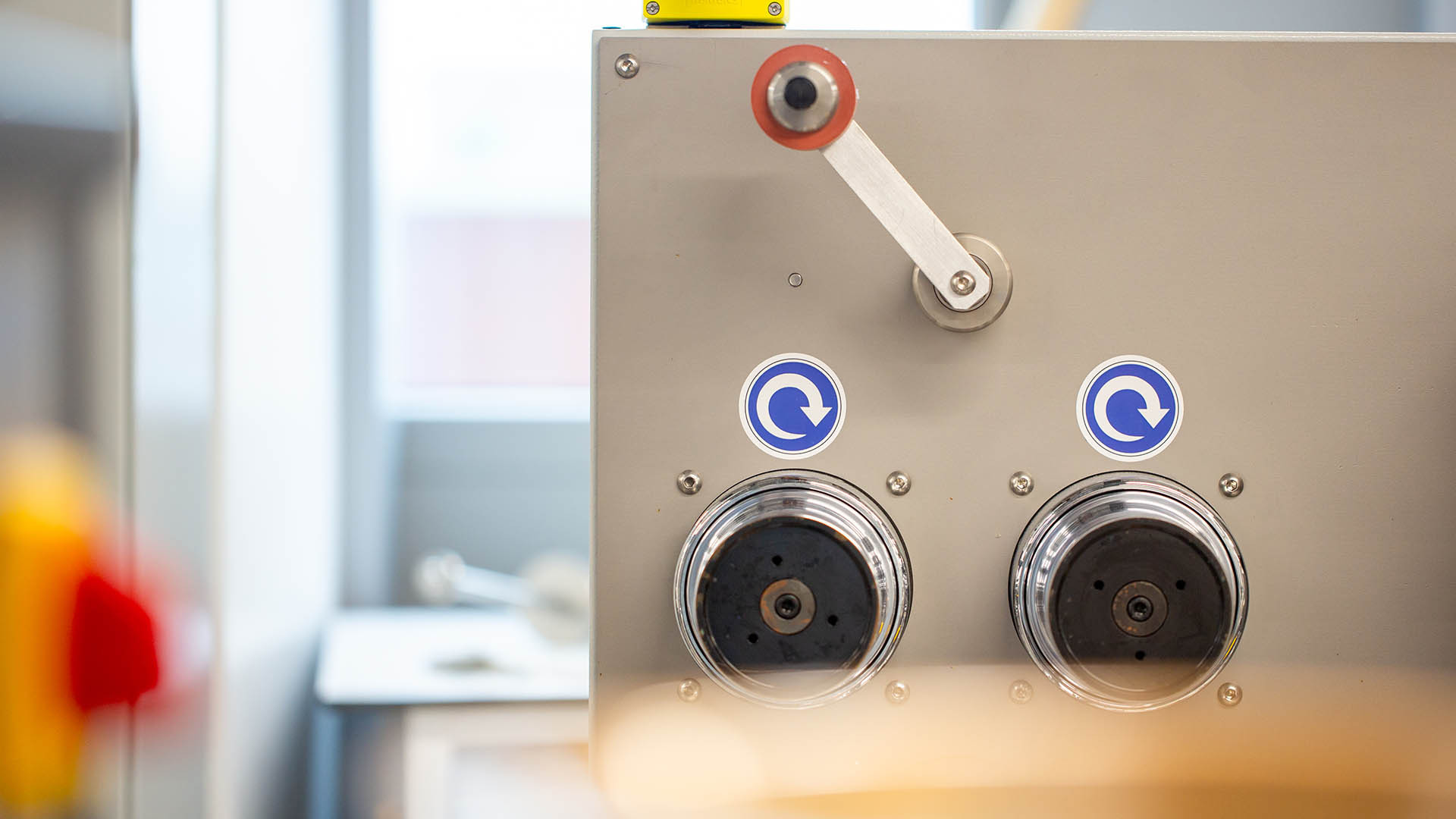
Key learning and future development
Several critical insights emerged from the trials. Firstly, drying control was crucial to prevent fibre shrinkage. Secondly, lignin solutions became more viscous over time, requiring adjustments to maintain quality. And thirdly, spinneret design affected fibre uniformity, highlighting the need for further refinement and development of the facility.
Through the project the team successfully produced continuous fibres. The next steps include refining fibre drying, collection, and carbonisation processes, which will be essential for scaling up this breakthrough technology in the UK.
A milestone for sustainable carbon fibre
51¸£ÀûÉç’s success in scaling up this novel technology marks a significant step toward commercially viable, sustainable carbon fibre production.
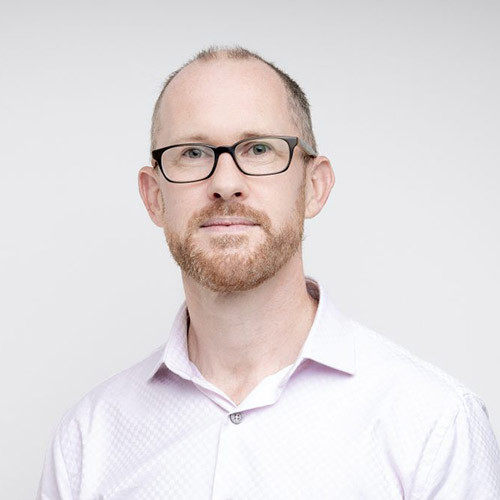
We're excited to use our capability to show the scale-up potential of this pioneering process to create a low-cost, renewable alternative to conventional manufacturing. Thanks to the equipment and expertise available at our pilot facility we were able to scale up Imperial's laboratory proof of concept to produce continuous fibres using lignin from Lixea, addressing key challenges in formulation and fibre drying, while also ensuring it could work with Lixea's wood fractionation technology. This trial represents a significant step toward making cost-effective, renewable carbon fibre a reality.
The future of carbon fibre innovation
With continued advancements and industry collaboration, lignin-based carbon fibre could soon become a commercially scalable, high-performance, and environmentally friendly alternative to petroleum-derived materials. 51¸£ÀûÉç’s pioneering role in technology scale-up reinforces its position as a leader in materials innovation and sustainable manufacturing, helping new ideas emerging in other UK leading universities, such as Imperial, make real-world impact.
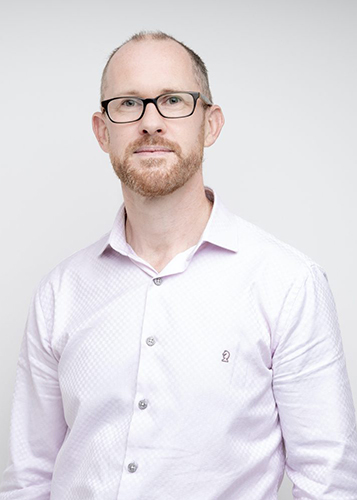
Meet the researcher
Jonny Blaker, Professor in Biomaterials, principle research areas are i) Bio-inspired hierarchical composite materials and ii) Advanced materials derived from synthetic biology, with an emphasis on medical applications. He currently leads projects on bioactive medical materials, mask-less digital photolithography for 3D printing/patterning surfaces, development of bio-inks for 3D printing/biofabrication, the exploitation surfaces and interfaces for materials production, processing of fibres, especially nanofibres via solution blow spinning including silks derived from synthetic biology, as well as shape-morphing composites.